Phoenix 3D Printing is a radically different manufacturing process. Unlike traditional methods, which cut, cast, or mold parts, 3D printing builds layers to create lightweight geometric objects.
Once a model is designed, it’s “sliced.” Slicing software scans the model to tell the printer how to make each layer of the object.
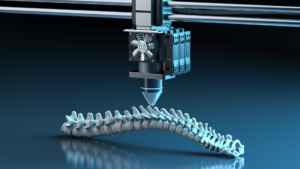
Rapid prototyping is a set of techniques that allow product designers to fabricate scale models of a physical part or assembly using computer-aided design data. These prototypes can then be used for testing and evaluation, allowing engineers to make better-informed decisions regarding the final design. The results of these tests help avoid potential production issues, speed up the time-to-market, and improve the quality of the finished product.
3D printing allows for a high degree of flexibility in fabricating these prototypes. Engineers can change the size, shape, or color of a prototype quickly and easily without requiring the use of expensive tools or materials. This makes the prototyping process much less risky than other production processes. If a prototype fails to meet requirements during the testing phase, it can be changed without the expense of retooling.
For example, if a component does not fit inside a mold, the engineers can simply print an entirely new component, rather than having to go back and redo the entire design. This can eliminate costly redesigns and reduce overall production costs.
The ability to create and test different prototypes in a relatively short amount of time is also helpful for getting buy-in from stakeholders. This can be particularly important if the product is being developed for a client, since the client may not be able to read CAD files or drawings. Being able to hold an actual prototype in their hand and see the changes that are being made will make it much easier for them to understand the impact of the change on the design and how it fits with the original objectives for the product.
Another advantage of rapid prototyping with 3D printing is the ability to produce a prototype with features that would be difficult or impossible to produce using traditional methods. For example, 3D printed prototypes can be made with thin walls and sharp corners that might be difficult to machine using CNC machining or sheet metal fabrication. The layer-by-layer nature of the printing process also means that engineers can quickly produce prototypes with complex geometries that aren’t possible to create with traditional tooling.
Rapid Manufacturing
3D printing (also known as additive manufacturing, AM) is a process that adds layers of material to a computer-generated design. The printer builds up the desired object layer-by-layer using a heated print bed and a range of materials. This contrasts with traditional machining and end-use part production processes, which remove material from a block of raw material to create the finished product.
This approach to product creation is highly effective for rapid prototyping, which often involves creating multiple iterations of a single design to gather customer feedback. Unlike traditional processes, which require expensive molds and weeks or months of lead time to produce a new component, a 3D printer acts as the mold and tool for producing a prototype, reducing costs significantly.
The speed and ease of 3D printing is especially valuable for creating functional prototypes, which focus on demonstrating and testing the product’s functions. For example, Melbourne-based Quad Lock has used their 3D printer to create over 100 iterations of a vibration-dampening smartphone mount for motorcycles in just one day.
Advanced 3D printing technology offers high precision and superior detail, allowing for the creation of accurate and complex prototypes. The high-resolution printing capabilities of technologies like PolyJet, FDM, SLA, and P3 DLP provide the capability to create prototypes that accurately replicate CAD data with intricate details and superior surface finish.
With this superior quality, it is possible to manufacture functional and aesthetic prototypes that are ready for mass-production, enabling companies to reduce the cost and time of bringing products to market. In addition, 3D printing allows for the creation of parts with geometric shapes that would be difficult or impossible to manufacture using traditional methods.
While 3D printing is often associated with the Do It Yourself (DIY) culture of amateurs and hobbyists, it has rapidly evolved into a powerful tool for industrial use and production. The flexibility of these systems enables designers and engineers to execute quick revisions of their designs with less risk, making it possible to bring new products to market faster. For manufacturers, this can translate into increased revenues and lower operational expenses compared to traditional manufacturing processes.
Reusable Parts
Pro: Fast prototyping saves Engineering time. With 3D printing, Engineers can quickly create and test design ideas, making changes almost instantly and eliminating the need for multiple steps in the production process. This allows for a faster turnaround from prototype to finished product and reduces overall manufacturing costs by eliminating part tooling.
Con: Complex designs can be difficult to print. While this is not always a problem with traditional subtractive manufacturing techniques, it can be an issue with 3D printing. Fortunately, this is a relatively easy problem to solve as 3D printers use a layer-by-layer approach to building parts and products. This ensures that each step is properly printed, eliminating issues like voids and inaccuracies. This helps to make sure that the end result is exactly what was envisioned in the design.
In addition, the fact that the layers are printed in a very controlled environment makes it easy to create intricate geometries and lattices that would be impossible or at least extremely difficult to produce with other methods. This enables a level of customization that allows for everything from aerospace industry components to personalized prostheses.
Another advantage of 3D printing is that the materials used to build the final parts are generally recyclable. This can be accomplished either by recycling the waste from the printing process itself, such as the supports used to prop up overhanging parts or old prints that were not up to scratch, or by using a service that recycles plastics into new spools of filament for 3D printing. This can significantly reduce waste and cost by eliminating the need for large stock inventories of parts that are not in demand.
This type of JIT manufacturing, or digital warehousing, can be a significant advantage for companies that require replacement parts to be available on-demand. It can also allow for rapid response to unexpected problems, as well as compensating for interruptions in supply chain. This can lower maintenance costs, improve reliability and cut inventory and delivery expenses by eliminating the need for storage of spare parts in warehouses and reducing transportation costs.
Sustainability
While 3D printing isn’t as environmentally friendly as traditional manufacturing, it does have a lower impact. This is because manufacturing processes require a lot of energy to create something small.
A large part of that comes from the energy used to heat or melt the materials used to make a product, as well as for cooling. When choosing which materials to use, it’s important to consider a product’s carbon footprint. This is the total amount of greenhouse gases produced by a material throughout its entire life cycle, including production, use and end-of-life. According to Ingeo, a company that provides biodegradable 3D printing filament, PLA (polylactic acid) has the lowest carbon footprint, followed by PET and ABS. It’s also important to consider a product’s embodied energy, which is the amount of energy it takes to make a material from raw materials. Ingeo notes that the manufacturing process for PET, ABS, and PLA can generate significant amounts of embodied energy.
Another factor is the reduction in waste. Traditional manufacturing is a subtractive process, meaning that you start with a block of material and hack away what you don’t need. 3D printing, on the other hand, is an additive process, building layers of a product. This results in exponentially fewer scraps.
In addition, 3D printing allows for a customized approach to production that reduces the need for stocking or overproduction of products. It’s particularly useful in locations that only need a certain number of parts on demand, such as military bases or remote mining operations. This can also help companies cut down on storage costs and minimize the need for transportation, which in turn cuts down on carbon emissions.
Lastly, the ability to print replacement parts extends the lifespan of an existing product, further reducing the need for new purchases and lowering overall energy consumption. In fact, some printers, such as the Nexa3D line of printers, allow you to recycle or repurpose unused powders, which further cuts down on waste and saves on resources.
While the sustainability of 3D printing is still an ongoing issue, it can be a valuable tool to solve specific problems. For instance, the construction industry can significantly reduce its environmental impact by printing specialty steel parts on site wherever they’re needed. This eliminates the need to transport heavy materials and helps mitigate wasted construction materials. It’s also a viable solution for the aerospace industry, which uses lots of metal to build aircraft, space shuttles and more.