Concrete is one of the most common and durable materials used in homes and businesses. However, it’s not indestructible. Concrete surfaces can sink, become uneven, and cause hazards if not addressed quickly.
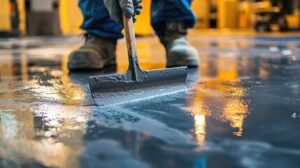
One solution is Concrete Leveling Bismarck. It involves pumping a slurry mixture underneath sunken concrete to lift it back up. This is less expensive than tearing up and replacing the slab and is safer than older methods like mudjacking.
Concrete leveling is a far more cost-effective alternative to having new concrete slabs poured. Replacing existing concrete can easily cost five times more than simply leveling it. Leveling also saves on the cost of demolition and removal services as well as landfill fees.
Leveling is performed using a unique technique that lifts and levels the surface rather than replacing it. Depending on the method chosen, prices range from $3 to $10 per square foot. It’s important to get precise estimates from a trusted contractor so that you can budget accordingly.
There are a number of factors that influence concrete leveling costs, including the type of damage that’s present and the size of the affected area. Larger areas require more materials and labor, which can drive up overall costs. In addition, different methods require distinct materials and equipment, which can affect the final price. For example, stone slurry grout leveling may require more intensive labor and more expensive material than foam concrete leveling.
Uneven concrete surfaces are not only unsightly, but they can be a safety hazard as well. If your sidewalk, driveway, or patio has become uneven, it’s important to have it repaired by a professional concrete leveling company. This will ensure that the surface is safe and secure for people to use, as well as protect your home’s foundation.
If you’ve noticed any of the signs of uneven settling, it’s important to act quickly. Not only will this reduce the cost of repair, but it can also help prevent further damage to your property. Uneven settling can lead to structural problems that affect the entire home, so it’s important to catch the problem early and have it fixed before it gets worse.
Concrete leveling with polyurethane foam is a cost-effective and effective solution for addressing uneven concrete surfaces. This process can repair cracked, sunken, and sinking concrete surfaces without the need for replacement. It’s an excellent option for homeowners who want to restore the beauty of their outdoor spaces and increase their property’s value. It’s also a great choice for business owners who need to provide their employees and customers with a safe and attractive walkway or patio.
Time
Concrete is found in a number of locations on properties, from sidewalks and patios to pool decks and foundation slab floors. Although the material is durable, it can crack and become uneven over time. This can not only look unsightly but also pose a safety hazard for those walking on the surface. In such instances, concrete leveling can restore the concrete to its original condition. Moreover, it’s cheaper than tearing up the sunken slab and pouring new concrete.
The first step to a successful concrete leveling project is a thorough inspection of the area. This can help spot any underlying problems that require attention before the repair process starts. It’s best to hire an expert to perform this inspection, as they can offer advice on the ideal solutions for the problem. For example, a professional can advise whether or not mudjacking or foam leveling is a better option.
Mudjacking and polyurethane foam are two common methods for restoring sunken or uneven concrete surfaces. Both can be performed in a few hours and have minimal impact on surrounding areas. Mudjacking involves pumping a clay/mud mixture beneath the concrete to lift it, while foam leveling uses high-density polyurethane that expands under the concrete to provide support.
Both concrete leveling techniques are less expensive than removing and replacing the sunken slab. However, the results of these repairs may not be as long-lasting as a replacement slab. Therefore, it’s a good idea to contact a concrete repair specialist as soon as you notice any signs of damage.
During the concrete leveling process, it’s important to protect the area from excessive moisture and temperature fluctuations. Doing so can prevent the self-leveling concrete from adhering properly, which can cause it to shift or crack once it’s fully cured. It’s also a good idea to test the concrete’s hardness before putting any weight on it. Finally, it’s essential to allow enough time for the compound to cure before resuming normal use of the surface. Taking these precautions will ensure that the concrete is strong and durable.
Safety
Concrete is used all over our homes, and it’s an important part of our daily lives. However, it’s easy for concrete surfaces to become damaged and unusable over time. Concrete leveling is a cost-effective repair method that restores sunken slabs to their original position and prevents future damage.
While the process is simple, it requires careful planning and execution. During the pre-project phase, it is crucial to assess potential risks and prepare contingency plans for unforeseen challenges. A detailed project plan also ensures that all work is completed according to specifications and meets safety requirements.
Before beginning, it’s critical to clear the area of any debris or obstructions. It’s also a good idea to check the ground conditions for stability and ensure that the surface is free of frost or water. During the pour, it’s vital to monitor the temperature of the mixture and use heaters to warm the mix. This will help improve hydration and prevent freezing.
Another essential aspect of the concrete leveling process is to take care not to overload the mixer. This can cause the concrete to set prematurely, which can result in an uneven surface and potential injuries. It’s also important to allow sufficient curing time, and to follow the manufacturer’s suggested curing times. Lastly, it’s essential to choose quality materials for the job, and avoid cheaper options that may not last as long or be as durable.
Despite the challenges of concrete leveling, this method is a highly effective solution for homeowners with sunken or uneven slabs. The results are both aesthetically pleasing and structurally sound, and they’re often more affordable than full slab replacement. It’s also a permanent solution, unlike patching and filling. In addition, it can enhance the safety and functionality of outdoor spaces, which is a major benefit for homeowners and their families.
Appearance
Concrete is one of the most durable and common building materials, but it’s not invincible. Over time, concrete can sink and become uneven, leading to unsightly appearances and safety hazards. Concrete leveling is a process that uses specialized equipment to lift sunken concrete and return it to its original position, restoring aesthetics and ensuring structural integrity. Modern methods also incorporate innovative materials like high-density polyurethane to achieve better results and durability.
The type of concrete used for leveling depends on the severity of the problem and the customer’s preferences. Generally, the best option is limestone concrete leveling, which is less expensive than new concrete and looks natural in any environment. Another option is polyfoam injection or foam leveling, which involves injecting a polymer under the concrete to fill any voids and raise it back to its original position. Polyfoam injection or foam leveling is also much faster and cheaper than mudjacking, and it provides a permanent solution that is resistant to moisture and sunlight.
When choosing a concrete leveling contractor, look for one with a history of proven success. An experienced company will have a team of experts who understand the challenges that can arise during the leveling process and how to solve them. They will be able to provide you with a free estimate and recommend the best repair method for your needs.
Besides repairing uneven surfaces, concrete leveling can also be used for a variety of other purposes. For instance, bridges and tunnels require precise leveling to ensure proper weight distribution across the slab. This will help preserve the structure over time and ensure a safe load-bearing capacity for passengers and vehicles.
It’s important to act quickly when you notice signs of sunken or uneven concrete. If left unattended, these problems can lead to costly repairs and even structural failure. Contact a local concrete leveling expert as soon as possible to receive an accurate diagnosis and advice on the ideal repair method. Depending on the extent of the damage, you may need to consider other repairs like resurfacing or repouring.